Reducing Defects, Increasing Throughput: Fisher Smith Ltd. Optimises Wavin UK’s Production Line
Introducing Wavin
Wavin UK (now Orbia) is a manufacturing company specialising in drainage products, specifically plastic pipes, seals, and guttering. They are committed to delivering high-quality products to their customers and maintaining a competitive edge in the market. However, they faced several challenges in their production process that hindered their ability to achieve optimal efficiency and quality. Fisher Smith Ltd. has a long-standing relationship with Wavin, having inspected their parts for outsourced suppliers since 2003, and then for their in-house production since 2010.
The Challenge: Defining the Problem
Wavin UK experienced several key challenges in their manufacturing operations at their Chippenham, UK site. These included:
- High rate of product defects, primarily "short shot" and "flash" on the rubber TPE section of their combined cap and seal products (110mm or 160mm diameter joiners).
- Fluctuations in product quality on an hour-by-hour basis due to material and temperature changes in the moulding process, as well as mould wear.
- Lack of a system to quickly identify and react to faults, which could result in thousands of defective products being manufactured and requiring extensive batch inspection and quarantining.
- The quality issues led to product failures in operation and reputational damage, as Wavin prides itself on producing reliable products with long lifespans, some designed for 90-100 years underground.
- Existing manual inspection methods were not scalable to meet increasing production demands.
Wavin’s Objectives:
To address these challenges, Wavin UK sought to implement a machine vision solution with the following objectives:
- Guarantee the quality of the product, ensuring all products were defect-free.
- Reduce scrap levels by capturing defects as they happen and enabling quick process adjustments.
- Automate the inspection process to remove manual labour and achieve a "lights out" operation for extended periods.
- Reliably detect key defects.
Our Approach: Understanding the Client's Needs
We began with a comprehensive assessment of Wavin UK's existing production processes and challenges. This involved understanding that the critical defects were predominantly on the TPE or rubber side of the products.
The Proposed Machine Vision Solution
Based on the assessment, we designed and implemented a customised machine vision solution that included:
- A 3D camera system was chosen to overcome the challenge of varying product colours, specifically black plastic with black rubber, where standard 2D vision would lack sufficient contrast. The 3D camera allowed for reliable separation of the rubber edge from the plastic background.
- Cognex VisionPro Deep Learning Library was implemented for image processing, analysis, and defect detection. This was a crucial choice as it could cope with part variations (e.g., slightly oval or non-round parts) that led to false rejects in previous rule-based inspection systems. Deep learning enabled reliable detection of "short shot" and "flash" defects and identified product orientation for targeted inspection.
- Integration with Wavin UK's existing Programmable Logic Controllers (PLCs) using Mitsubishi SLMP protocol for real-time control and feedback, including changing running jobs for different product colours and sizes.
- A customised user interface developed with Cognex Designer, featuring access controls for operators.
- A database was created to log all inspection data, allowing the end customer to extract and analyse it for future optimisation.
- Specialised optics were used, including a blue, speckle-free laser for improved image quality and reduced environmental impact.
- Different sets of lights for 2D inspection were incorporated to optimise images for new colour variations, an upgrade from previous systems.
Consultancy and Expertise Applied
We provided expert guidance and support throughout the project, including:
- A deep knowledge of the product and moulding process, which was crucial for concentrating inspection on likely fault areas.
- Strong understanding of Cognex deep learning software to choose the right tools for defect detection.
- On-site visits and close collaboration with the machine builder partner to integrate hardware, confirm communication with the PLC, and acquire images from parts moving through the automated system.
- Extensive deep learning training, involving labelling and teaching various fault types, to ensure accurate separation of good and bad parts.
- Addressing technical challenges such as interference between lighting of the two cameras through spacing, electronic separation, and physical shielding.
- Working with the client to generate new faults and challenge the system with "hot" parts, which behave slightly differently than cooled parts, to ensure robust performance on good production and achieve a very low false reject rate.
- Comprehensive training for Wavin UK's operators on interacting with the system, visualising defects, and interpreting data.
- Providing remote access via secure VPN for quick support and issue resolution.
- Continuous communication and collaboration to implement UI improvements based on operator feedback.
Implementation and Execution – A Seamless Integration
We ensured a seamless integration of the machine vision solution into Wavin UK's existing production line. This involved:
- Careful planning and coordination with Wavin UK's production team.
- Precise installation and calibration of the system components.
- Thorough testing and validation to ensure accuracy and reliability.
- Development of custom interfaces for data exchange between the machine vision system and Wavin UK's other systems.
- A full turnkey, fixed-price project approach.
Collaboration and Communication
Importantly, we maintained a collaborative and communicative approach throughout the project, including:
- Regular project meetings and clear documentation.
- Prompt response to inquiries and proactive communication of potential issues.
Key Achievements
The implementation of our machine vision solution delivered significant results for Wavin UK, building upon the benefits of their previous automation systems:
- Vastly improved false reject rate: The deep learning system achieved a false reject rate of less than 0.1%, a massive improvement compared to the previous systems' 1-2% on fresh products and over 10% over time. This meant virtually no good parts were being rejected.
- Reduced material waste: By catching defects quickly and accurately, the system significantly reduced the amount of mixed-polymer scrap, which cannot be reworked or recycled and typically goes to landfill, leading to cost and environmental savings.
- Improved confidence and reliability: Operators now have high confidence in the machine, as almost all products in the reject bin are legitimate defects, eliminating the previous issue of good parts being falsely rejected.
- Enhanced ability to react to faults quicker: The system enables immediate detection of faults, preventing thousands of defective products from being manufactured before manual batch inspection would identify the issue.
- Valuable insights for process optimisation: The system provides real-time data on machine wear and production throughput, allowing Wavin to feed this data back into their moulding process to optimise quality at the source and further reduce scrap.
Qualitative Benefits
In addition to the quantifiable results, Wavin UK also experienced several qualitative benefits, including:
- Improved product quality and consistency, enhancing their brand reputation.
- Increased employee satisfaction due to the improved efficiency and reliability of the machine, making day-to-day production smoother for operators.
- Greater confidence in their ability to meet customer demand and maintain their reputation for high-quality products.
Wavin Testimonial
Wavin UK has expressed great satisfaction with the low reject rate compared to their other machines, confirming multiple times that all products in the reject bin are legitimate, which has significantly built confidence in the vision system.
Summary of Success
Our successful implementation of a customised machine vision solution at Wavin UK demonstrates their ability to deliver significant and measurable results for manufacturing companies. By addressing Wavin UK's specific challenges and providing expert guidance, Fisher Smith Ltd. enabled them to achieve their objectives, improve their operations, and enhance their competitive position through the innovative use of deep learning technology.
About Fisher Smith
Fisher Smith Ltd. is a trusted partner for manufacturing companies seeking to optimise their production processes through machine vision technology. Their deep expertise, comprehensive solutions, and commitment to client success make them a valuable asset for businesses looking to improve quality, efficiency, and profitability. Fisher Smith Ltd. combines cutting-edge technology with practical experience to deliver solutions that are tailored to each client's unique needs, as demonstrated by their continuous innovation and ability to improve upon legacy systems. Their solutions are highly reliable for plastic inspections and can be generalised across various plastic manufacturing defect types.
To learn more about how Fisher Smith Ltd. can help your manufacturing company achieve similar results, please contact us today for a consultation, or call us on +44 (0) 1933 62 51 62.
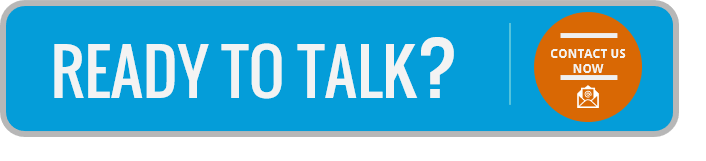