Fast automated inspection of seals through 3D vision with HALCON
Brett Martin is a producer of different plastic solutions like, amongst others, push-fit products in the area of plumbing and drainage. They hired us to develop an automated inspection system, which inspects the caps and seals of push-fit products.
The Challenge
Each bend, reducer or joint has a cap fitted with a rubber seal that seals the cap to the pipe but also allows the mating part to be sealed to the inside diameter. As these products are used e.g. in the sewage system of houses, i.e. underground, a long lifetime is required.
The inspection requirement mainly applied to “short-shots”, where the dosed plastic respectively rubber is too low, so that the mould is not completely filled and the product has a gap at the end. This “short-shot” looks like a dent or notch in the circular seal and would cause a leak. The plastic is black, white, brown or grey with black rubber. Since there is no contrast, the black rubber is difficult to distinguish from the black plastic.
One requirement of the customer was to integrate the new system into the existing one. The inspection should be performed when the robot of the existing system takes the parts out of the moulding machine and places them on a cooling conveyor. Depending on the result, whether positive or negative, the robot then places the parts in the appropriate places for further processing or sorting out.
The Solution
3D vision was the ideal solution to check the relative height of the rubber compared to the plastic, mainly because of the necessary distinction between black rubber and black plastic.
We chose the Photoneo PhoXi 3D Scanner for Brett Martin primarily because it was able to deliver high quality images that were significantly better than the competition. Using our own software was the ideal solution. GenVis is based on MVTec’s machine vision library in HALCON and due to its ready-to-use interfaces to hundreds of industrial cameras and frame grabbers, we could choose from a wide range of machine vision cameras and scanners as well as different brands and technologies. We could then quickly integrate the Photoneo PhoXi 3D Scanner into the software as HALCON supports the corresponding interface. In this way, we were able to use the standard tools they already had to further process the tested parts accordingly.
The robot presents each part to the scanner. The acquisition of each image takes less than one second, then the robot moves on to the next part. Eight parts are made every 20 - 30 seconds.
The Benefits
The main advantage of this solution is the significant reduction of faulty parts that reach the end customer. In addition, the new system could be easily integrated into the existing processes without slowing down production or losing production space inside the cell.
Text and images kindly provided by Photoneo.
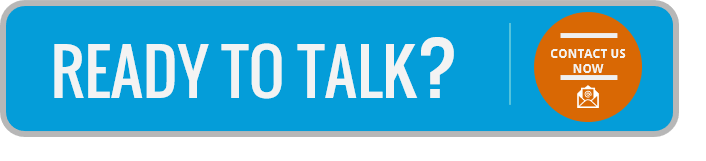